Product Information
The RigiMill MG has achieved a chip removal rate of 1,200 cubic inches (19.7 liters) per minute in aerospace aluminum and is available with an automatic pallet system up to 950″ (24 m)!
RigiMill Moving Gantry (MG) was developed to produce the fastest chip removal rates in the world. Various spindle configurations achieve chip removal rates up to 55 cubic inches/min (0.9 liter/min) in titanium and 1,200 cubic inches/min (19.7 liters/min) in aluminum, this machine makes it possible to use the same machine for high speed roughing and finishing. Equipped with a single spindle, high speed gantry, the RigiMill MG provides the highest quality and precision of machining either aluminum or hard metals.
It is the unique architecture, as the most compact ever gantry structure with monobloc heavy cast iron bridge structure, as well as, its “no Ram” design through vertical moving cross-rail that offers the most rigid spindle thanks to constant overhang feature, and make the RigiMill MG as being a formidable “beast of efficiency”. Learn more about the impressive speed and strength of RigiMill MG through the informative article RigiMill vs. Traditional Multi-gantry Machine, where the machine is compared to traditional multi-gantry machines. This comprehensive comparison showcases the distinctions between the RigiMill and traditional multi-gantry machines.
The RigiMill MG purposely reduced scale is an innovative design solution that offers new achievable performances compared to existing machines in the market. It can be configured to each customer’s specific needs and can be extended in the X-axis direction after installation. RigiMill MG is the best manufacturing platform in the world for long part production machining!
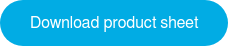
CASE STUDY: Machining single aisle aircraft wing stringers
From 630” (16 m) aluminum extruded profiles to finished accurate single aisle aircraft stringers: MODIG Technology
MODIG RigiMill MG machines produce 164,050 ft (50,000 m) of single aisle aluminum wing stringers every month worldwide. These typical long and slim parts made of aluminum or titanium alloys are processed on MODIG RigiMill MG with no length limits. A 630” (16m) aluminum wing stringer was previously machined with a well-known multi-machining center in 205 minutes. How fast is it machined in RigiMill MG? Read the article for more details and to learn about the significant time savings achieved.
Our solutions – your advantage!
The all new RigiMill summarizes much of the spirit and ambition that keep us going here at Modig. Developing and producing high-tech machining solutions at the frontline of what is possible, always with the benefits of our clients on our mind. That is what it is all about, and that is what RigiMill exemplifies.
Join the Modig community!
Are you keeping up with the amazing technology releases at MODIG?
Subscribe to our newsletter and receive the latest news of webinars, products and more!
