Product information
The HHV (Horizontal High Velocity) was developed in close cooperation with the world’s largest aircraft manufacturers. Since its introduction, it quickly became the first choice of top performing machine shops.
The HHV is a universal machining center for bar or extrusion components. It is ideal for limited production runs, nesting, or high-volume production. Raw material is loaded from the left side into the machine, the HHV automatically pulls the raw material into position for machining and delivers finished parts into a part catcher. Instead of cutting raw material into specific lengths, the HHV handles uncut bars and extrusions. The benefit of making many parts from the same size bar or extrusion is: reduced setup time, no workholding, and a significant reduction in cycle time. Standard machining often requires multiple setups. The HHV machines parts complete in one setup, with no work holding.
Your machining cycle time at the process design stage: up to 50% faster machining time over conventional processes, and, true Lean and Green production. Discover more about Learn more about the exceptional MODIG bar machining process by reading the article, Bar Machining. The Modig Way VS. Conventional Machining.
HHV 2 and HHV 3 designates the number of rotary tables.
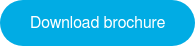
“We guarantee 40% cycle time reduction with the HHV”
– David Modig, President Modig Machine Tool
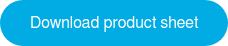
Preventive Maintenance: The Key to Optimal Machine Performance
Regular preventive maintenance is crucial for maintaining the optimal performance of your machine over time. By consistently conducting preventative maintenance, monitoring the status of your machining center, and replacing worn-out parts and consumables, you can guarantee that your machining center remains in excellent condition and can operate with the same precision and speed as when it was brand new. In our article Preventive Maintenance. Give Yourself Peace of Mind you will learn more about preventive maintenance and how to find the wear parts and consumables you need to ensure your HHV is ready to Keep up.
Join the MODIG community!
Are you keeping up with the amazing technology releases at MODIG?
Subscribe to our newsletter and receive the latest news of webinars, products and more!
