Lowest cost per part
Mill-Ex is a high-speed milling machine with 2 spindles individually driven in all three axes. With up to 1.5G acceleration and high feed rates, it is well suited for the demands of aluminum machining.
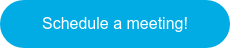
Smallest footprint on the market for multi-spindle machines!
A key benefit is machining parts in one setup with a 2 spindles – higher part throughput with lowest cost per part. Typical parts are aluminum components for automotive (cross member, battery tray, body-in-white) aerospace (floor beam, wing rib, airframe), electronics, and many other applications. The Mill-Ex manufacturing solution offers the opportunity to customize the solution with for example different coolant options (high-pressure coolant, MQL, or dry milling) and loading/unloading (manual or automated by overhead gantry robot or by 6-axis robots from the front). Mill-Ex provides the ability of loading new raw material while machining with the benefit of no unproductive time. The low cost of ownership makes Mill-Ex a very competitive solution.
High Part Throughput. Lowest cost per part!

Streamline Your Workflow with Automation for Mill-Ex
Consider adding automation to your Mill-Ex machine tool. We provide various solutions, from standalone automation to complete production cells for workpiece handling – All from One source. Our all-in-one approach simplifies your implementation process and ensures that our automation solutions seamlessly integrate into your workflow.
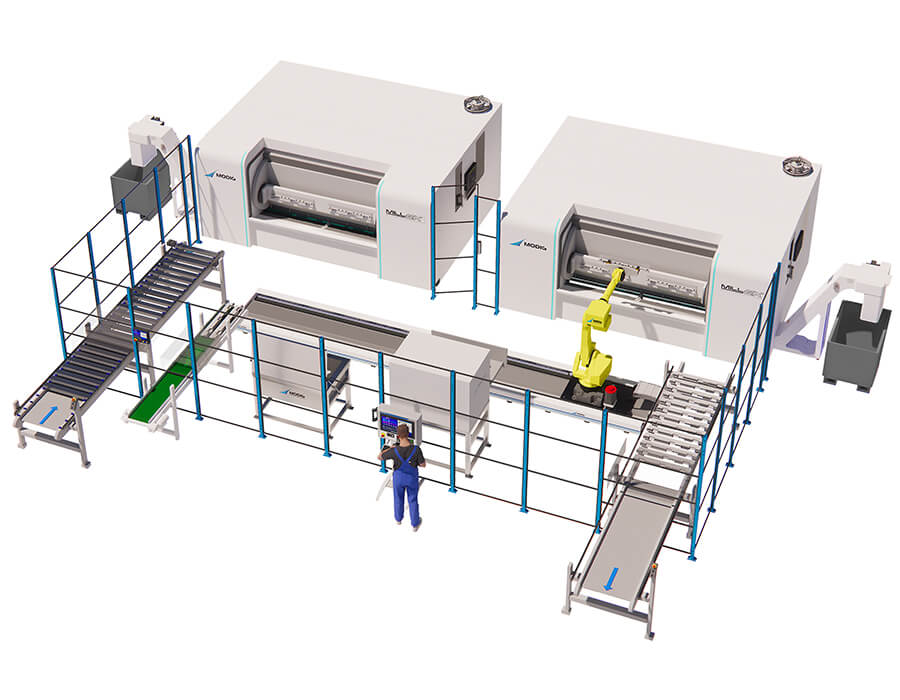
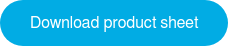